"The combination of NI VeriStand and the NI PXI platform meets the needs of users for I/O, computing power, signal emulation, and data analysis, and is completely open and modular." – Enrico Corti, Alma Automotive.
This article refers to the address: http://
challenge:
Based on commercial off-the-shelf (COTS) hardware, a modular hardware-in-the-loop (HIL) test system is developed for real-time simulation of engines and complete vehicles to reduce the number of physical tests required during embedded software verification.
solution:
Test systems based on NI VeriStand real-time test software and NI PXI hardware provide the computing power you need to implement high-speed control with field-programmable gate array (FPGA) hardware, while different I/Os not only guarantee The HIL system can meet current needs and can be expanded to meet future application needs.
Alma Automotive is a company based in northern Italy that provides customized solutions for the calibration, control and testing of automobiles. Alma Automotive offers pure software (model or model-based analysis) or integrated hardware and software solutions based on customer needs. Eldor offers automotive electronic components such as coils, sensor systems and electronic control units (ECUs).
Because HIL systems can be used to automate and standardize tests, they are the standard for ECU testing. Most of the HIL systems available on the market offer standard features that cannot be extended or customized. Eldor chose the HIL solution proposed by Alma Motors because the hardware and software of the solution are open and can be based entirely on their Customization of requirements.
The HIL system emulates the equipment controlled by the ECU, and all actual signals entering the ECU must be replaced by signals generated by the HIL test system. Because the goal is to test the functionality of the ECU, the simulation must run in real time. The model must accurately respond to ECU commands to test the entire embedded control system. For some types of signals, it is difficult to reproduce a correct time base because the high frequency signal needs to be synchronized with the instantaneous position of the crankshaft. Typical examples of this include cylinder pressure, accelerometer, ion current, and intake pressure signals.
There are many HIL systems available on the market today. The main disadvantage of most systems is the lack of tools for customizing the underlying libraries provided by HIL vendors, making it difficult to access underlying (like FPGA) functions, so these systems are not able to meet customer needs.
The combination of NI VeriStand and the NI PXI platform meets the needs of users for I/O, computing power, signal emulation, and data analysis, and is completely open and modular. Two key factors that determine the success of the application are the ability to leverage the NI LabVIEW FPGA Module to create complex FPGA code and the creation of a custom device to output camshaft, crankshaft, intake, sensor current, and in-cylinder pressure signals.
The HIL system (Figure 1) proposed by Alma Automotive integrates the following hardware and software components:
一个 A complete engine/vehicle/motorcycle/driver model developed with PXI real-time controller with a step time of 500μs and a single-core CPU load of 20%;
一个 A high-bandwidth signal generator implemented with custom equipment that is used to generate model-based crankshaft, camshaft, intake, in-cylinder pressure, and ion current signals, as well as to capture all ECU output commands Including ignition, injection, H-bridge and interrupt lights. This custom device is implemented with the 7852R board.
一个 A custom I/O signal conditioning board designed and manufactured by Alma Automotive to convert the ECU analog output signal into a TTL digital signal and, if necessary, enhance the analog output signal of the PXI 6723 (variable reluctance signal, VRS) ).
定制 A custom actuator and sensor fault insertion unit (FIU) designed and manufactured by Alma Automotive and an external junction box that provides 96 signals.
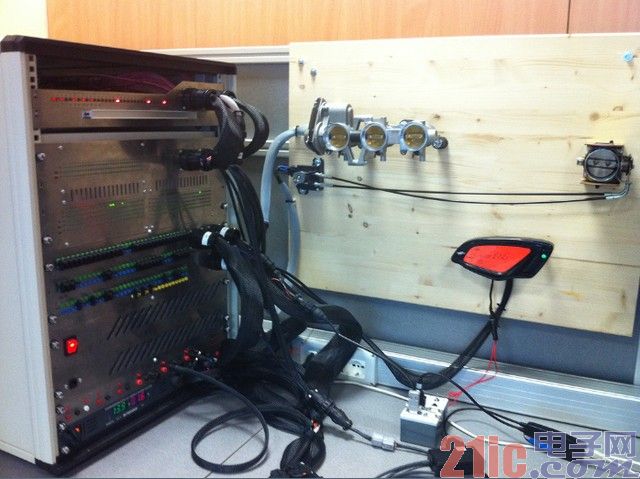
Figure 1 HIL system integration
The vehicle simulation mode can be used for open loop (user driven vehicle) or closed loop simulation (driver follows vehicle speed trajectory). The dynamometer mode can also simulate the operating conditions of the test rig. The engine uses a multivariate torque map to model the engine's torque, air/fuel ratio, and other parameters. These outputs are sent to a custom device to generate high frequency signals, such as an intake pressure signal. Engine torque is used to provide vehicle and transmission submodels, powertrain components. Engine and vehicle speeds are calculated based on engine torque, clutch position, plug-in gears, tire operating conditions, and actual loads on the front and rear wheels.
The driver submodel manipulates the steering wheel, brakes, clutches, and shifts via torque-based control logic, while the dynamometer sub-model calculates the torque provided to keep the engine running at the required speed and load operating conditions. There is also a heat exchange submodel to evaluate the engine coolant temperature; the electrical system submodel allows the user to simulate the starter and battery voltage levels during startup.
At the heart of the system is the NI VeriStand custom device plug-in designed by Alma Automotive. The plug-in is an engine I/O subsystem simulator that produces dual-channel VRS/Hall sensor signals with signal-conditioned peak-to-peak voltages up to 120V, angle-based configurable waveforms, and 4-channel wheel signals. It also acquires 12 channels of conditioning high voltage ECU excitation signals; 16 channels of universal high voltage ECU output signals such as on/off, frequency and PWM; and 8 channels are tuned to analog input signals in the 120V peak-to-peak range. Figure 2 shows the setup interface for this custom device. The number of teeth of the sensor wheel and the type of sensor wheel are fully configurable.

Figure 2 Customized Crank Reference Signal Generator Equipment
The FIU developed by Alma Automotive is also based on FPGAs, which use FPGAs to process more than 400 signals that require operation of the switch. The determinism of the FPGA allows security functions to be set in the system, including user-defined fault timeouts, global FIU disables, and overcurrent monitoring on the faulty bus. The FIU operation after the break is prevented by the user-configurable load release delay to prevent ambiguous states in the faulty channel.
Developed by Alma Automotive, the FIU can handle up to 64 channels with access to four common fault buses with a maximum current limit of 2A. Open GND, Vcc, and VBATT can be used as power supplies. The feedback information of the switch status can be obtained by 320 LEDs.
Users can connect to the actual load as well as the simulated load. When an actual load is used, such as a throttle, the simulation system reads information from a feedback sensor such as a throttle potentiometer and supplies it to the model. When using a simulated load, such as a virtual throttle, the feedback signal is generated by an emulator, such as an analog output channel, and sent to the ECU. Switching between the actual load and the simulated load is done by moving the jumpers on the external junction box.
The system was successfully connected to the target ECU. Figure 3 shows a typical NI VeriStand interface for HIL testing.
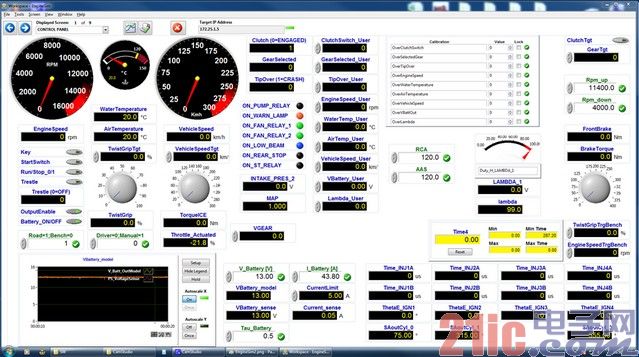
Figure 3 HIL test control panel
Users can use the existing methods and bench test modes to focus on verifying the software and hardware capabilities of all ECUs. Easy to use and configure, users can perform system reconfiguration directly without requesting customer support. The NI PXI platform is ideal for integration with third-party custom development boards.
It is important that the hardware and software of the HIL test system be continuously updated as needed. Because NI PXI hardware is modular and based on COTS components, it can be easily upgraded, which ensures that the system will work in the future and ensure technology leadership. With an open architecture and easy integration with LabVIEW and other development software, NI VeriStand provides the flexibility needed to address any challenges that may arise as testing requirements change.
Product features:
â– Good heat dissipation
--Blade design of copper alloy contacts,good conductivity
â– Super high impact resistance and thermal stability
--Cover pans are made of high quality polycarbonate
â– Chemical corrosion resistance
-- Fingerprint-resistant zinc plated mounting brackets
â– Grounding
--One-piece grounding design,No Load-Weather resistance
Generator TR&WR GFCI UL,Electrical Plugs UL,GFCI Sockets for Generator,Self-test Generator TR&WR GFCI UL
Hoojet Electric Appliance Co.,Ltd , https://www.hoojetgfci.com