Signal level conversion problems and advantages
An input/output voltage that fails to reach the power supply level will reduce the signal noise margin, and precise timing of the signal will also cause duty cycle distortion problems. Input signals that exceed the maximum input level can cause excessive power consumption, which is especially undesirable in battery-powered systems. In the worst case, overvoltages can even cause device failure. Signals in excess of the maximum level of a few hundred mV are enough to damage a microprocessor.
Given that the signal is in the form of a rail-rail and in most cases, a single device, the dual-rail device is the simplest, most reliable, and most efficient use of space conversion (Figure 1). However, dual-rail converters also have some commonly used alternatives, each with its own advantages and disadvantages.
Figure 1 Dual-rail device between processor and camera IC in a cellular phone
Sometimes it may not be necessary to use a special conversion circuit. When a device with a lower voltage has an over-voltage tolerant (OVT) input, a one-way, high-to-low transition can be used. An OVT buffer or bus switch can also be added to the signal path to provide this functionality. In this application, the OVT buffer has the advantages of simplicity, low cost, and low power consumption. However, for bidirectional conversion, the low voltage output signal must cross the high voltage input switching threshold. Disadvantages include duty cycle distortion and a reduction in the high voltage side noise margin (Figure 2).
Figure 2 Adds an OVT-enabled transceiver between the processor and the peripheral IC. The 2.0V signal from the transceiver and processor achieves amplitude matching, and the signal noise margin from the transceiver to the peripheral is also very small.
For applications that require a low-to-high or bi-directional conversion level, an open-drain buffer can be combined with an external pull-up resistor. With this method, the buffer operates at a lower voltage, and the output level is set to a high voltage by using an external pull-up resistor (each output has a pull-up resistor). Although the two-way and low-to-high conversion problems can be solved, this approach also increases the number of components, board space, power consumption, and often affects duty cycle distortion.
Custom converters can also be designed based on discrete field effect transistors (FETs). Custom designs have the flexibility to provide accurate bit widths and the power required; however, customization also increases the number of devices. As assembly costs increase, system costs and board space requirements increase. Customization also drags down design time, increasing the risk that development schedules will not be completed on time.
The most reliable and convenient option is the dual rail converter, which guarantees the correct input/output voltage on both sides of the device. The signal level can be set by connecting a separate power supply pin to the appropriate power supply. Thus, the converter input/output levels can be changed correspondingly to the supply voltage. The two-rail converter eliminates design and cost challenges by providing a proven, off-the-shelf device that allows the designer to configure the input/output signals at each end of the component to exactly change to the desired voltage while minimizing The number of additional devices needed. Problems caused by voltage swing, such as not reaching the signal level, or exceeding the rated value, will be eliminated.
Problems to consider when designing a dual-rail conversion system
Although the two-rail converter provides the simplest method of voltage level conversion, its implementation is still problematic. Double-track converters are becoming more and more convenient, and they are becoming more and more diverse. However, different vendors and products will have different device performance specifications and functionality. When considering the use of a converter in the system design, the performance of the device must be taken into account.
The impact on the system timing is one of the major issues that need to be considered. Buffers add propagation delays to the system. Due to their complexity, this propagation delay is important for dual rail converters, especially for older processes, or when the conversion needs to span a wide voltage range. When the amplitude of the conversion is less than 1.5V, the propagation time may exceed 10 ns. Since speed is an important factor, new converter products will reduce delays.
Another parameter that system designers need to consider is the output driver. Most dual rail converters are driven at 3.3V (24mA) high voltage, allowing components to be used in applications requiring cable or line-drive applications. However, in general, the drive current is proportionally reduced as the device's power supply voltage is reduced. The device rated at 3.3V with an output drive of 24 mA may provide only 6 mA at 1.9V. The design of the output load and timing budget must take into account the relationship between supply voltage and output drive.
For devices with dual power supplies, the last issue to consider is the order in which power is applied to the VCC and control pins. The converter control pins are powered by one of the dual supplies. Therefore, most converters require a certain order of power supply for each supply and control pin. If power is applied to the input/output pins first and then applied to the control pins, uncontrolled oscillations may occur. If the control pin is powered down first, the same problem will occur. Possible results of this uncontrollable state include: excessive power consumption and system damage. Therefore, the order of power-up and power-down must be strictly guaranteed. The new converter product allows the output to remain in a high-impedance state before both supplies reach an effective level, thus solving the problem of power supply sequencing.
Conclusion
Although there are other methods that can be used for signal level conversion of dual supply devices, their use is limited to one-way, high-to-low conversions, while other options require multiple discrete components to solve the conversion problem. For space-limited, low-to-high or bi-directional conversion applications, these methods are not the best choice. By using a dual-rail converter to implement the design, it is possible to ensure that the conversion is error-free and that the system is protected from damage. The dual power converters ensure that the signals on both ports reach the full swing, eliminating problems with voltages above or below the voltage limit, and provide a simple, space-saving conversion method to meet any performance aspect demand.
LED point light source is a new kind of energy conservation and environmental protection decorative light, using LED cold light source, the built-in microcomputer chip, can be arbitrary programming control, multiple synchronous change, monochromatic changes can also be realized synchronous colorful gradient, jump, scanning, running water light color change effect and multiple LED point light source form a lattice screen.All kinds of pictures, text and animation effects can be changed. It is a supplement of linear light source and flood lighting, which can meet the design requirements of the point line surface.
Product size
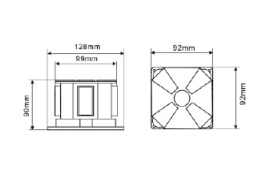
Led Point Lamp,Blue Point Led Lamp,Led Point Ovale,Led Blue Point
Jiangsu chengxu Electric Group Co., Ltd , https://www.satislighting.com