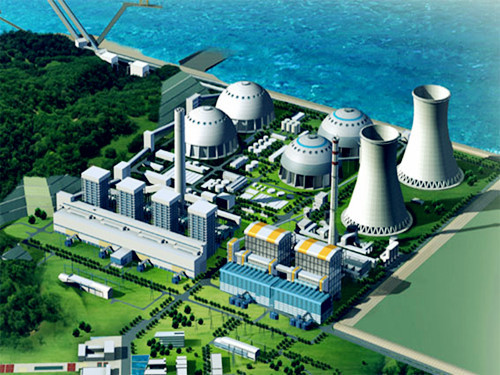
At present, China has more than 1 billion kilowatts of electricity generating capacity, with coal power accounting for close to 70% and generating electricity exceeding 75%. The fact that coal-fired electricity is a major part of China's electricity is difficult to change for a long period of time in the future. How the existing thermal power technology achieves low-carbon operation has become a consensus of the international community. Internationally, supercritical and ultra-supercritical technologies have matured, creating conditions for improving the overall efficiency of thermal power in China.
In order to make our country's thermal power units more efficient and cleaner, we have shut down approximately 10 million kilowatts of pure condensing steam-type high-energy-consuming units with a capacity of less than 200 MW per year since 2004. In addition, the government has also adopted large-scale introduction of imported technologies and localization methods to convert the main models of newly-built thermal power units into 600-1000MW supercritical and ultra-supercritical units.
Constantly refresh energy saving records
As the first batch of 1000MW ultra-supercritical projects in China, the Shanghai Waigaoqiao Third Power Plant (hereinafter referred to as the “External Three Power Plantsâ€) project was completed in March and June 2008 respectively, and two units were built and put into operation. In 2009, the foreign three power plants created a world record low of 282 g/kWh for power coal consumption.
In order to fully enhance the overall performance of the unit, during the construction of the project, the external three power plants have carried out a large number of optimization and technological innovations in the aspects of project design, equipment selection, construction and commissioning, start-up and operation, etc. The net efficiency of the performance test is 45.03% (circulating cooling water temperature 19°C), far exceeding the design level and the same type of unit in the same period. In the year of production, with an average load rate of only 74%, the average net operating efficiency reached 42.73%.
After the unit was put into operation, the external three power plants further developed a series of new energy-saving and emission-reduction technologies with “zero-energy desulphurization†and “energy-saving all-weather denitrificationâ€, which were implemented through annual unit maintenance opportunities, and the efficiency and environmental protection of the two units. Every year can be significantly improved. At present, the net efficiency of the unit (including desulfurization and out-of-stock) has reached 46.5% or more, which is equivalent to the expected efficiency of the next-generation 700°C high-efficiency supercritical unit still under study abroad.
As we all know, the loss of the boiler accounts for about 80% of all losses. Therefore, how to reduce this loss is most important. In addition, the induced draft fan and desulphurization booster fan work to make the flue gas enthalpy and temperature rise, the temperature rise up to about 10 °C, quite considerable, but the waste heat recovery device is prone to surface condensation of sulfuric acid dew, a strong corrosion of the heat exchanger At the same time, the fly ash in the flue gas can easily stick to the surface of the decomposed heat exchanger. The alkaline soot is cement-like after being combined with the sulfuric acid dew, and it is extremely difficult to remove.
In order to solve this problem, the external three power plants through special control measures, as far as possible so that no condensation on the surface of the heat exchanger, coupled with the heat exchanger in the low-temperature steel has a certain degree of acid resistance, and place it in the booster fan The low dust area between the desulfurization tower can not only prevent the wear, but also reduce the risk of dust accumulation and clogging. It also takes into account the recovery of the exhaust fume from the induced draft fans and booster fans. Heat exchangers use finned tubes to increase heat transfer efficiency. The heat recovery working medium is condensed water between the low pressure heaters, and the heated condensed water reduces the extraction of the low pressure cylinder and reduces the heat consumption of the steam turbine.
The desulphurization flue gas waste heat recovery systems of the two units were put into operation in June and October 2009, respectively. After many inspections, the corrosion situation is very slight and the impact of life is negligible. The performance test showed that the production of the unit increased the efficiency of the unit by 0.4%, and the water spray of the desulfurization tower was reduced by 45t/h.
Digging equipment to save energy
For newly-built power plants, including new power plants whose equipment types have been completed, some of the conventional measures to improve efficiency have become inoperable. In order to effectively improve the efficiency of power plants under the existing technology platforms, the external three power plants seek to reduce the possibility of various types of related losses from the equipment and systems.
To this end, the foreign three power plants completed the implementation of a series of major technological innovation projects. For steam turbines only, technological changes such as optimization of main steam parameters and operation adjustment methods, optimization of feed water pumps and systems, and energy conservation have been adopted.
In order to avoid opening the steam inlet valve under normal circumstances, the external three power plants will appropriately increase the design pressure of the main steam and set the overload opening point of the steam inlet valve to the maximum cooling water temperature in the summer for the two cases of the steam inlet valve. The load ensures that the steam inlet valve will not be opened at rated load and under the following conditions throughout the year. At the same time, for the normal load section of the turbine operation, research and development of successful energy-saving extraction frequency modulation technology to speed up the reaction, so that the power adjustment range becomes larger. It is estimated that the above two optimization and innovation measures can increase the unit efficiency by approximately 0.22%.
For the first time, three external power plants in China use a 100% steam-powered feed pump, which is equipped with an independent condenser and can be started separately, eliminating the electric feed pump. The start-up steam source is obtained from the cold reheat steam of the adjacent unit, which greatly reduces the energy consumption during the start-up phase of the unit. For Alstom’s dedicated small-scale turbine for feed pumps, a steam source with cold and reheat steam was added to adjust the door and the corresponding adjustment stage, which maximized the operating efficiency of the unit at rated operating conditions. Researched and tested successful technologies of low-speed start-up and full-speed operation of the steam-powered water pump group, which greatly reduced the energy loss at the start-up of the boiler and improved the unit efficiency and equipment operation safety.
At the same time, the external three power plants have developed corresponding series of technologies based on the generalized theory of regenerative heating. The full application of this technology can increase the unit operating efficiency by more than 0.42%. Through the expansion of water supply and heat recovery technologies, the developed elastic regenerative technology can be used at 75. Under the load of %, increase the unit operating efficiency by 0.2%.
In addition, as an ultra-supercritical unit, the increase of steam parameters, especially the increase of temperature, steam side oxidation of the pipeline and the resulting solid particle erosion, pose a serious threat to the safety and economic operation of the unit. Through more than 10 years of tracking and research, the External Three Power Plants have achieved a series of breakthrough results. Based on this, they have formulated a comprehensive set of prevention and control technologies and strictly implemented them in the construction of the external three power plants. After 30 months of operation, the external three power plants carried out pipe cutting inspections on the boiler's three-stage superheater and two-stage reheater's pipeline. The superheater and reheater pipes were smooth and smooth, without any oxide scale shedding and oxides. Accumulated phenomenon. Similarly, after 30 months of operation of the steam turbine, the comparison of the performance tests showed that the internal efficiency of the steam turbine has not changed since the first start of the unit.
At present, the foreign three companies have a new batch of major energy-saving innovations that have completed preliminary research and project planning. One of the world's first "freq power plant power conversion technology" project has been completed and put into production, the current plant rated power consumption under the conditions can be reduced to 1.7% or less. This technology can also improve the operating efficiency of the main steam turbine. In addition, there are new energy-saving and innovative technologies that will be implemented in batches in conjunction with unit maintenance. At that time, the energy efficiency of the two units in the external three power plants will continue to increase.
It is worth mentioning that high-temperature steam pipes are the biggest obstacle to the two reheating and 700°C plans that can significantly increase the efficiency of the unit. In response to this problem, the author proposed “a high-low steam turbine "Generator" design technology, adopts this patented technology, considers existing materials, considers 600°C grade steam parameters and secondary reheating plan, combines the energy-saving optimization and innovative technologies of the external three power plants, and includes generators for desulfurization and denitrification. Efficiency up to 49% (circulating cooling water temperature 19°C). Its unit cost can still be controlled at the level of existing primary reheat supercritical units, but the efficiency has far exceeded the current 700 °C plan's expected value, which is of great commercial value. The scheme currently has no technical bottlenecks. Whether it is a new unit or a large-scale transformation of an existing unit, the program is currently the best choice
SPI LED Strip Light including the WS2801, WS2811, USC1903, ect. led rgb pixel strip. It is 3 leds 1 pixel type digital led strip. 60leds/m and 30leds/m led addressable led tape are available. High quality and cheap price. widely used for outline profile decoration, clubs, pubs, and so on. With ISEELED Dmx Decoder, it also can work with Artnet and DMX control system. IP20, IP65, IP67 and IP68 led pixel flexible strip are availble.
Photo show of SPI LED Flexible Strip Light:
Spi Led Flexible Strip Light,Addressable Led Strip,12V Led Strip Lights,Multi Color Led Strip
Shenzhen Iseeled Technology Co., Ltd. , https://www.iseeledlight.com