Comparing today's portable consumer electronics to a few years ago, you will understand why lighting has become a major power management challenge. Handheld devices with a single passive LCD panel are rapidly being phased out. Today's devices feature high-performance, high-resolution, 2.5- to 3-inch diagonal color displays to support a full range of applications from Internet access and mobile TV to video playback.
Typically, these displays require four or more LEDs and drivers for backlighting. Many handheld devices (especially clamshell designs) have added a smaller secondary display to show basic information such as time, date and connectivity. These secondary displays typically require one or two more LEDs for the backlight function than the primary display.
As design engineers discover the importance of fashion lighting in product differentiation, many portable electronic devices today require additional power circuits to drive auxiliary RGB status lights and keyboard backlights.
The built-in camera feature features a more complex power circuit design. These functions typically provide a flash by driving a small number of LEDs at high current for a very short duration. But when handheld device manufacturers first introduced this feature, they used a CCD of less than 1 million pixels, which required the flash driver's current to not exceed 100 mA. Today's handheld design engineers are integrating a much higher resolution CCD that requires up to 600mA of current to be used only to drive the flash and provide enough light for high photo resolution. Newer features such as movie mode and flash function increase the design difficulty of the power circuit by requiring a lower level power supply to drive the LED for longer duration.
With these developments in mind, it's easy to understand why lighting is often the most battery-intensive source of handheld devices. Previously, design engineers used their boost converters or charge pumps to provide their lighting capabilities on a stand-alone basis. But as the number of lighting functions increases and power requirements increase, design engineers need better control to handle light intensity, manage color balance, and maximize power. Eventually these engineers turned to system microcontrollers or dedicated controllers to address these issues with pulse width modulation (PWM) control.
Simpler design
In recent years, power management integrated circuit (PMIC) manufacturers have developed various ICs designed to provide engineers with higher levels of control and simplified design. Take the National Semiconductor (NS) LM27965 as an example. This white LED (WLED) driver can drive up to 9 LEDs in parallel with a total output of up to 180mA. In order to maximize the control ability of the design engineer, the output forward current can be divided into two or three independent control groups, and four to five LEDs are configured to provide backlight for the main display; two to three LEDs are configured as sub-displays. The screen is backlit; a single independently controlled drive is configured to manage the status or indicator LEDs. Each set of LEDs is controlled via a standard I2C interface.
While solutions based on inductive boost converters still offer advantages in many applications. But in many cases, manufacturers are turning to hybrid mode or fractional charge pumps to drive WLEDs in compact portable applications, and no longer need large sensors. Although the output in a fixed boost charge pump is modulated with a separate resistor, LED current matching and efficiency may be affected. With a mixed-mode charge pump, the output voltage is modulated to maintain a constant current for each LED, allowing designers to more accurately match current sources.
Similar to many competing products, Linear Technology's LTC3219, released in August, uses a multimode charge pump that turns on in 1x mode and then when any enabled LED current source approaches voltage drop. Automatically convert to boost or 1.5x mode.
Wire Carrier & Tubular Carriers
Fabricated steel wire baskets and wire carriers are designed and manufactured using high quality steel tubing as well as sheet metal for the coiling of wire. A solid basket is often used in house for rod break-down and then used subsequently in wire drawing of large stranders for power cables. Wire carriers are used for coiling and packaging wire from wire drawing equipment, and are then used as in-house or shipping packages.
Wire Coiling Baskets
- Manufactured from high quality tubing
- Heavy duty construction
- Heavy duty construction
- Various sizes per application
- Standard sizes per coiler
- Manufactured from high quality tubing
- Light-to-heavy duty constructions
- Square, clover & star base
- Sizes as per request
Wire Carrier
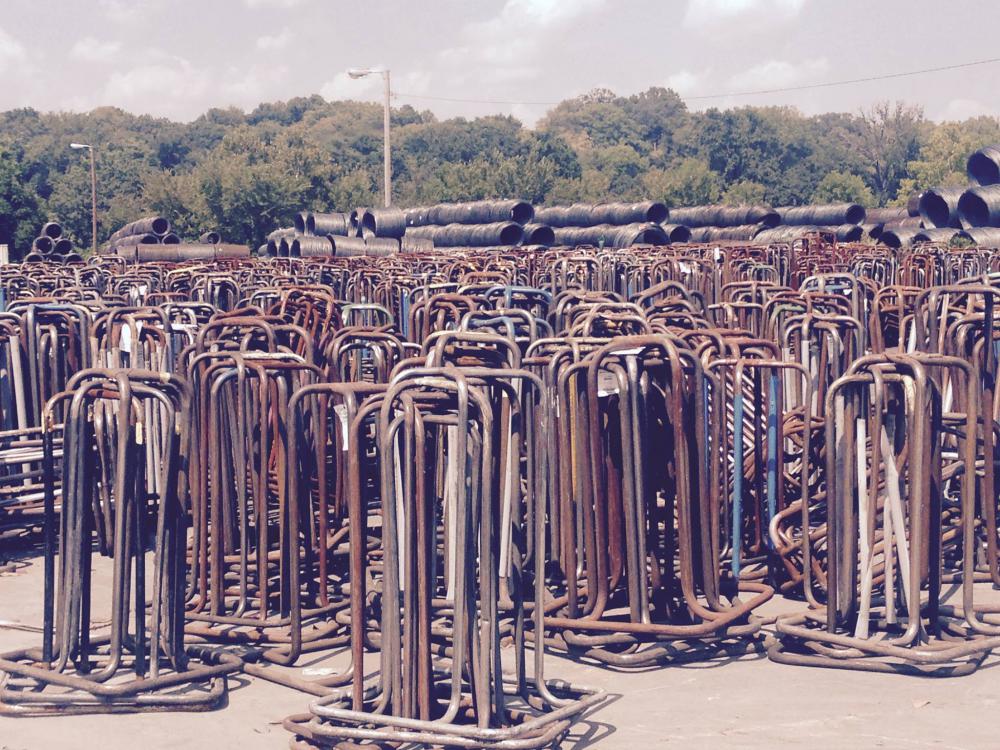
Wire Carrier
Coil Carriers, Cable Basket, Steel Basket, Steel Coiler, Wire Carrier
NINGBO BEILUN TIAOYUE MACHINE CO., LTD. , http://www.spool-manufacturer.com